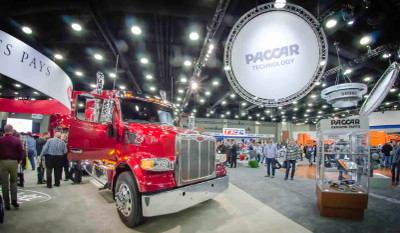
DSG's 4+ Fuel Additives Recognized by PACCAR
25.02.25
DSG's 4+ Fuel Additives Recognized by PACCAR
Injector failure can decrease engine performance, increase emissions, and lead to costly repairs in diesel engines. Regular use of 4+ Super Clean effectively prevents these complications, ensuring diesel engines' longevity and optimal performance.
PACCAR, a leading manufacturer of heavy-duty trucks and engines, recommends 4+ Super Clean Additive to safeguard against injector issues. Below is the Fuel Injector Cleaning Procedure for EPA21, MX13, and MX11 PACCAR engines. Please confirm the latest revision before each use.
When to Use
This procedure applies if the truck is equipped with an EPA21 MX13/MX11 engine and exhibits one or more of the following faults or symptoms:
- • Engine Knock
- • Fault Codes:
P3300, P0300, P0301, P0302, P0303, P0304, P0305, P0306
P1263, P1266, P1269, P1272, P1275, P1278
P0263, P0266, P0269, P0272, P0275, P0278
Parts Required
Fuel System Cleaner Fluids
- • (Preferred) DSG 4+ Super Clean #SKU: DK32P - 5 quarts. Available here
- • (Preferred) PACCAR Fuel System Cleaner FX9 #2281100PE - Available only in Canada through PPD
Fuel Lines and Container
- • PN2281101PE fuel system cleaning tool – 1 unit. Available through PPD
- • If PN2281101PE is unavailable, fuel line tool kit 1961366-1CH can be used to run the engine from a bucket.
- • If neither tool is available, alternative fuel module fittings and hoses can be used that allow engine to be run from a bucket.
Note: 5L container (compatible with PN2281101PE tool hoses) are available through:
- • Dynalon - https://www.dynalon.com/PublicStore/product/NEW-MultiCan-Barrier-Container-SL,918.aspx
- • Amazon - https://www.amazon.com/Dynalab-405404-0005-Carboy-MultiCan-Barrier/dp/B09BSGH6G6
- • Clean bucket can be used instead of the compatible 5L container
Fuel Injector Cleaning Procedure
Step 1: Collect DAVIE4 Data
- 1. Collect the DAVIE4 logfile before performing the cleaning procedure.
- 2. Perform and record the DAVIE4 "Evaluate the Injector Back Leak" test.
Note: Collection hoses do NOT need to be installed.
Step 2: Drain the Fuel Filtration Module
- 1. Unscrew the pre-filter screw cap until the O-ring is visible.
- 2. Within 30 seconds, unscrew the main filter screw cap until the O-ring is fully visible.
- 3. Wait at least 2 minutes for the filter bowls to drain completely.
- 4. Retighten fuel filter caps to 80 ± 5 Nm (59 lb-ft) per RMI.
Step 3: Install Fuel System Cleaning Tool
- 1. Disconnect the chassis supply and return lines from the fuel filtration module.
- 2. Connect the PN2281101PE tool supply and return lines to the module.
Step 4: Prime the System with Fuel System Cleaner
- 1. Fill a 5L container with John Deere Fuel System Cleaner and attach it to the PN2281101PE tool.
- 2. With the PN2281101PE supply line submerged in John Deere cleaning product, clean-up 2 diesel fuel system cleaner (either with the compatible 5L container or clean bucket. to prime the system.
- 3. Operate the hand prime pump for 1-2 minutes to prime the system.
Note: The cleaner must be used at full concentration. Do NOT dilute with diesel fuel.
Step 5: Perform the Fuel System Cleaning
- 1. Start the engine and run at idle for 1 minute.
- 2. Increase idle to 1200 RPM and run for 15 minutes.
- 3. Stop the engine and let it sit for at least 30 minutes to dissolve internal contamination.
- 4. Restart the engine, increase idle to 1200 RPM, and run for 10 minutes or until the cleaner is almost empty.
- 5. Stop the engine.
Step 6: Flush Cleaner from Fuel System
- 1. Disconnect the PN2281101PE tool supply line from the filtration module.
- 2. Reconnect the chassis fuel supply line.
- 3. Start and run the engine for 3 minutes or until the 5L container is full to flush the system.
- 4. Stop the engine.
Note: This step allows the engine to run from clean diesel fuel while returning contaminated cleaner into the container.
Step 7: Remove Cleaning Tool from Engine
- 1. Disconnect the PN2281101PE return line from the fuel filtration module.
- 2. Reconnect the chassis fuel return line to the fuel filtration module.
Step 8: Replace Fuel Filters
- 1. Replace both fuel filters according to the RMI procedure.
Step 9: Perform and Review DAVIE4 Tests to verify successful cleaning
- 1. Perform DAVIE4 "Verify Injector Calibration" procedure.
- 2. Perform DAVIE4 "Evaluate the Injector Back Leak" test.
- 3. Review the test results.
Note: The average unbalance of each cylinder should be ±6 RPM in the stable phase of the test (18-37 seconds).
Step 10: Check Stable Phase of Test
- 1. If, during the stable phase, the average unbalance of cylinder(s) deviates more than ±6 RPM and the engine still exhibits knocking or misfire faults:
- 2. Replace the injector(s) of the affected cylinder(s).
Step 11-Repair verification
- 1. Clear fault codes with DAVIE4.
- 2. Perform road test for final repair verification.
Fuel Additive Recommendation
To prevent future injector issues, PACCAR recommends using one of the following fuel additives:
Product | Part Number | Treatment Ratio | Additive per 50 Gallons |
---|---|---|---|
DSG 4+ Super Clean | DK32P / DK32 | 1:1,200 | 5.3 oz |
Power Service Diesel Kleen + Cetane Boost | 03025 | 1:500 | 12.8 oz |
John Deere Keep Clean | TY26827 | 1:1,280 | 5 oz |
Note: The use of additives is at the discretion of the customer.